선반/복합가공기주축 제조를 통해 보는
타협을 용납하지 않는 “제조”
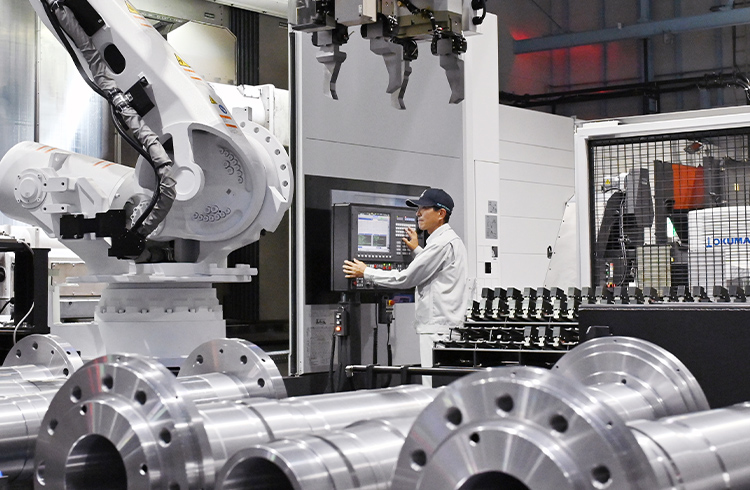
품질 기준이 1µm라도 벗어나면 불합격
「공작기계의 심장부인 주축 제조에 대한 오쿠마의 고집은 레벨이 다른 것 같습니다」라고 말하는 것은 입사 이후, 30년 이상 선반 가공에 종사하며 「아이치의 명장」에도 뽑힌 가츠다 요시히로(勝田佳裕)씨입니다. 그는 배속된 주축 가공부문에서 기능을 연마하며, 선반・머시닝센터・연삭반・복합가공기의 본체 주축에서 문형머시닝센터의 어테치먼트, 특수 공구의 설치 주축에 이르기까지 모든 종류의 주축 가공을 담당했습니다.
주축의 제조공정은 소재의 절단→단조→선삭 황삭가공→딥홀가공→소준(Normalizing)처리→선삭 마무리가공→머시닝가공→방탄・침탄처리→황삭 연삭가공→마무리가공의 순서로 진행됩니다. 그 과정에서는 소재의 재질, 열처리 방법, 변형교정, 마지막 연삭가공까지 각 공정의 중요한 포인트에서 엄격한 품질 기준・가공 기준을 세워 정도를 체크하고 있습니다.
「품질 기준이 1µm라도 벗어나면 불합격입니다. 오쿠마의 품질 기준을 지키기 위해, 최종적인 마무리 가공은 반드시 사내에서 실시하고 있습니다」라며 카츠다는 밝힙니다. 이렇게 완성한 주축과 관련 부품은 유닛 조립부문에서 정밀하게 조립되어 (본 사이트 CASE2 참조), 본 기기에 탑재됩니다.
항상 뛰어난 정도로 깎을 수 있는 기계이기 때문에
결코 저렴하지 않은 공작기계를 도입하는 것이므로 항상 뛰어난 강성과 가공정도를 유지해, 가공품질과 생산성 향상에 공헌하기 바란다 —— 이것은 모든 고객의 공통된 바램입니다.
그러나, 현실적으로는 「같은 기계에서 황삭가공과 마무리가공을 병용하고 있으면 무엇인가 부조・문제점이 발생한다」 「중절삭과 경절삭을 반복하고 있으면 치수의 불균형이 눈에 띈다」 「공정집약을 위해 하드 터닝 가공을 하고 싶지만, 주축이 견딜 수 없을 것이다」・・이러한 것들은 주축이나 베어링 등의 가공・조립 정도에 기인한 강성 부족, 기계 본체의 구조를 요인으로 하는 강성 부족 등이 원인일 수 있습니다.
오쿠마는 이러한 현상과는 무관한 고강성, 고정도의 기계를 제공하는 것을 설계・제조의 기본 이념이라고 자리매김해, 엄격한 품질관리를 철저히 하고 있습니다.
실제로 아시아 지역의 판매대리점 기술 서비스 지도와 협력회사의 기술 지도를 위해 대만의 제조 자회사에 주재한 가츠다씨는 고객으로부터 들은 말을 지금도 잊을 수 없습니다. 「오쿠마 기계는 10년 사용하다 보면 고강성, 고정도의 진가가 보인다」 「오쿠마의 기계를 도입해 회사가 발전했다」 「언젠가는 카탈로그의 표지를 장식하고 있는 5축 가공기와 복합가공기를 도입하고 싶다」・・.
이러한 고객의 한마디 한마디가 마이스터를 비롯해 오쿠마 전직원에게 커다란 격려가 되고 있음은 말할 필요도 없습니다.
마이스터의 가공 노하우를 지능화기술에
오쿠마 기계라고 하면 고강성, 고정도와 함께 제품 제조 환경을 혁신하는 「지능화기술」이 알려져 있습니다. 예측 가능하도록 열변위하는 ・충돌하지 않는 ・채터 없는 ・최적화된 가공조건으로 자동조정… 이러한 고정도・고생산성을 지원하는 혁신적인 가공 인프라 기능은 오쿠마의 가공 현장에서 쌓아온 마이스터들의 암묵지(요령, 포인트)를 수치화해, 디지털 제어함으로써 실현한 성과입니다.
선삭의 마이스터인 가츠다씨가 그 일례로서 장척 워크에서의 채터 억제에 대해서 해설해 주었습니다. 「장척물은 같은 회전 수로 절삭하면 아무래도 채터가 발생합니다. 그러나, 기능공들은 워크의 재질・형상이나 공구를 판별해, 부하를 거는 방법, 회전 수를 조정해 채터의 발생을 억제합니다. 이 기술을 NC 제어에 반영시켜 최적화된 가공조건을 이끌어내는 것이 「Machining Navi」입니다」.
또한 「지능화기술의 대표라고 할 수 있는 열변위를 정확하게 제어하는 「Thermo-Friendly Concept」도 고정도의 부품 가공과 조립 기술이 있어야 성립하는 기능입니다. 환경 온도나 가공에서 발생하는 열 변화에 의해 기계가 “예측 가능하도록 변형하기”때문에 제어하기 쉽다. 따라서 같은 구조를 채택해도 오쿠마 기계 정도의 가공정도를 낼 수 없는 것은 기계 제조방법이 다르기 때문입니다」라고 .
선배로부터 후배에게, 오쿠마의 제품 제조
마이스터가 되기까지의 여정은 어떠한 것이었을까. 가츠다씨는 「배속되는 곳마다 나중에 명장이라고 불리는 선배가 있어 도면에서 최적화된 가공 공정과 순서를 이끌어가는 수법, 풍부한 지식과 응용력, 낭비 없이 정확하고 스피디한 근무 자세 등, 모든 것을 배웠습니다」라고 말하는 자신도 주축 가공뿐만 아니라 전・후공정의 지식도 자연스럽게 흡수. 한층 더 폭넓은 기종에 관련된 가운데 납입기의 설치 업무에 종사해, 다능공으로서의 역량을 높여 갔습니다.
현재는 이러한 경험을 토대로 「제품 제조 가공 도장」의 강사로서 중견 사원 실습생을 대상으로 몸에 익힌 모든 기능을 전수하려고 분투하고 있습니다. 목표는 실습생의 국가기능검정 100%의 합격률과 다능공의 육성입니다. 그 때문에 사내 기능경진대회에서는 젊은 층의 가공 교육에도 힘을 쏟아, 기능의 최저 수준 향상을 도모하고 있습니다.
「언젠가는 오쿠마의 신예기를 도입하고 싶다」는 고객의 기대를 뛰어넘는 제품을 제공하기 위해 도장에서는 오늘도 젊은 실습생들이 기계와 워크를 마주하고 있습니다.
오쿠마의 장인
금속공작 기계공
가츠다 요시히로
- 1985년
- (주)오쿠마 철공소(현 오쿠마(주)) 입사
- 2000년~2001년
- Tatung-Okuma Co. Ltd(대만) 주재
- 2007년~
- 아이치현 기능검정 검정위원
- 2015년
- 아이치의 명장에 선출
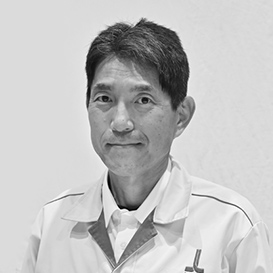