모두가 무모하다고 한「기계와 환경의 열변위 제어」에 도전
고정도로 절삭하기 위해서는 가공 시에 발생하는 다양한 열변위에 대응해야 하며, 신속하게 가공하기 위해서는 진동에 대처해야 합니다. 그러나, 공작기계의 긴 역사 속에서「열」과「진동」의 문제는 대단히 어렵고 영원한 테마로 여겨져 왔습니다.
특히 열은 번거롭고 주로 철과 주물로 되어 있는 공작기계는 온도가 1℃ 오르면 1미터당100분의 1밀리 팽창하며, 가공 시에는 주축과 주변기기에서 발생하는 열에 의해 기계 본체가 팽창합니다. 또한 일반적인 공장 환경에서는 10℃ 정도는 당연한 것처럼 변화해, 이로 인해 기계의 자세를 변화시켜, 가공정도에 영향을 끼칩니다. 공작기계 메이커는 주축과 주변기기의 열을 냉각유로 억제하는 대책을 강구하지만, 본질적인 해결은 되지 않았습니다.
그러한 가운데 우리는 1994년경, 핵심기술로서 주축의 열변위를 분석해 보정하는 보상시스템(주축 열변위 제어 TAS-S)을 개발해, 이것을 탑재한 머시닝센터에서 금형 가공을 하고 있는 고객을 조사하기 위해 방문했습니다.「주축의 열변위를 억제한 것만으로는 안됩니다. 대기업이 아니면 항온실의 설치 등은 무리입니다. 일반적인 환경에서 안정적으로 10μm 이하의 가공정도를 낼 수 있는 기계가 있으면 치수 보정작업이 편해지지만, …」이라는 갈망의 목소리를 들었습니다. 이것이 개발진에게 커다란 동기 부여가 된 것입니다. 그러나, 시시각각 온도 변화하는 공장 환경에서 안정된 치수 정도를 낼 수 있는 기계를 만드는 것은 무모한 도전이며, 주위에서는 비상식적이라고도 했습니다.
브레이크 스루의 계기는 발상의 대전환
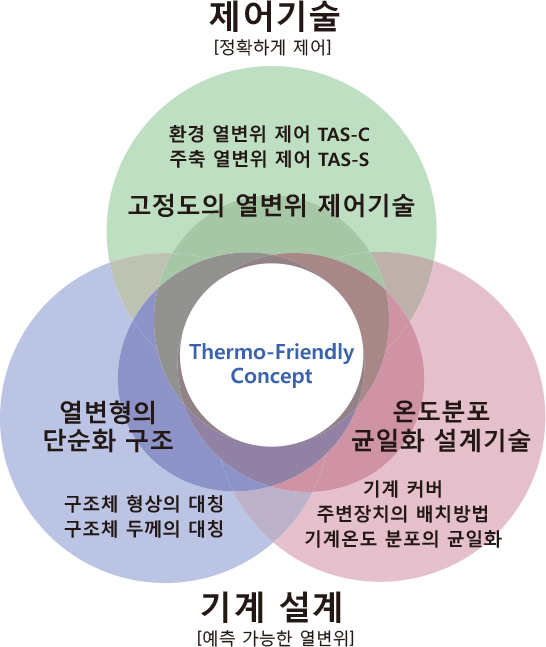
수년간에 걸쳐 다종 다양한 기종의 열과 구조를 환경 시험실에서 분석해, 방대한 데이터와 마주하는 가운데 확신한 것이「발열하는 기계나 실내 온도를 필요 이상으로 차게 하거나 단열해도 복잡해져 고비용이 발생할 뿐. 그것보다도 열변위를 제어하기 쉬운 기계의 구조를 밝혀내, 발생 열을 제어하는 쪽이 합리적이다. 열을 억제하는 것이 아니라 열을 받아들여 사이 좋게 한다(열전 접점 프렌들리)」는 발상의 전환이었습니다.
이렇게 해 다다른 것이 「① 굴곡이 없는 예측 가능한 열변위를 발생시키는 심플한 구조 ② 열원의 배치와 온도 밸런스에 대한 배려 ③ 리얼타임으로 열변위를 제어(보상)하는 시스템」이라는「Thermo-Friendly Concept」이며, 이것을 처음으로 제품화한 것이 수직형 머시닝센터「MB-46VA」입니다.
지금도 오해하시는 분이 많지만, 열변위 제어란 「발생한 열을 측정해 복잡하게 변형한 양을 보정하는 기술」이 아닌, 「제어하기 쉬운 열변위 밸런스가 뛰어난 기계 설계가 대전제이며, 이것을 토대로 열변위를 제어하여 안정된 가공 치수 정도를 실현하는 기술」입니다.
덕분에 시간 경과에 따른 가공 치수 변화 8μm를 실현한「MB-46VA」는 놀라움으로 맞이하여, 「치수 보정작업이 격감해, 안심하여 정도를 확보할 수 있다」라는 등 커다란 반향을 불러 일으켰습니다. 또한 타사에서도「클레임 문제였던 열변위를 이익이 나는 기술로 바꾼 것은 대단하다」라고 말합니다.
진화를 계속하면서 폭넓은 기종으로 전개
「MB-V」에서 얻은 반응을 원동력으로「Thermo-Friendly Concept」을 복합가공기, 5축 가공기, 문형기로 탑재를 확대해 갔지만, 진화의 전환점이 된 것은 복합가공기와 대형기(문형)로의 전개였습니다.
복합가공기는 주축이 늘어나는 가운데 상하부 터렛을 움직여, 대향 주축도 더해지는 등, 열원의 증가에 의해 변위가 복잡해져, 그 조합에 의한 바리에이션도 다양합니다. 개별적으로 열변위 보정방법을 바꾸어 버리면 도저히 대응할 수 없습니다. 그래서 어떠한 기종이라도 뛰어난 열변위 밸런스를 유지할 수 있는 수법을 확립하는 것으로 했습니다. 방대한 계측과 데이터의 분석을 기계 설계에 활용해, 제어도 심플하게 할 수 있는 기술 개발에 전력을 쏟아 크게 스텝업할 수 있었습니다.
문형기로의 전개에서는 높이가 수직형의 2~3배, 테이블 면적이 36배가 되는 기계에 워크를 올려 20μm의 가공정도를 타깃으로 열변위 제어의 혁신에 도전했습니다. 개발 당시, 이와 같은 대형기를 넣어 실험할 수 있는 항온실이 없어 자세 변화와 열팽창의 측정에도 고생했지만, 그 만큼 기계 설계와 제어 이론을 철저히 파고들었습니다. 그리고 이끌어낸 이론을 실증하기 위해 대형 항온실을 신설 및 평가해, 「MCR-BⅢ」의 탄생으로 이어졌습니다. 그리고 납품한 고객사 32곳을 방문해, 39대에 대해서 고객의 환경 하에 납득하실 수 있는 성능인지를 확인했습니다. 커다란 워크에서도 치수가 안정되어, 장시간의 가공에서도 가공 단차가 생기지 않을 정도의 사용하기 편리함을 실현할 수 있었던 것도 개발의 노고로부터 얻은 노하우의 성과입니다.
Thermo-Friendly Concept 탑재기의 누계 출하 대수와 기종 수
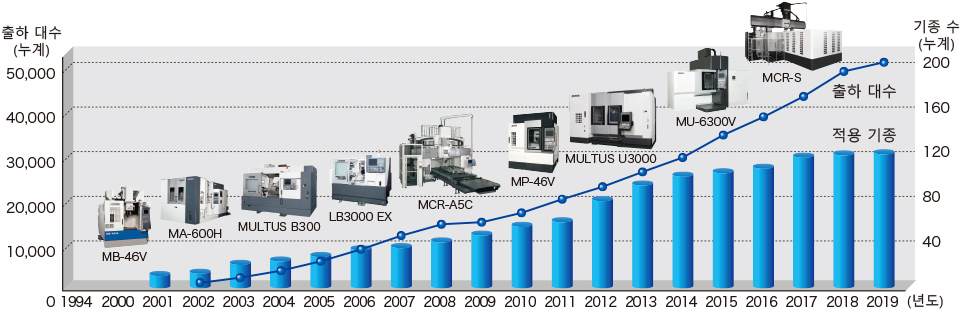
무인 자동 가공의 시대를 내다본 지능화 기술을 개발
오쿠마는 5개의 지능화 기술(Thermo-Friendly Concept, Collision Avoidance System, Machining Navi, 5-Axis Auto Tuning System, SERVONAVI)을 고객의 가공 인프라 향상에 기여하는 기능으로서 제공하고 있습니다. 실은 그 대부분이 「Thermo-Friendly Concept」을 개발했을 때에 「장래, 무인 자동 가공의 시대가 도래한다. 그 때, 공작기계 메이커로서 어떠한 기능을 준비해야 하는지」를 테마로 철저히 의논해 핵심 기술을 체계화한 것입니다. 우리는 그것을 순차적으로 구현해 왔습니다.
5축 가공기계를 예로 들면, 아무리 열변위 제어가 뛰어나도 회전축의 중심 오차가 발생합니다. 이에 대응해 기하오차를 간단히 조정하는「5-Axis Auto Tuning System」을 개발한 것입니다. 5축 가공기에 처음으로「Thermo-Friendly Concept」을 탑재한「MU-500V」는 호평을 받았습니다. 또한,「5-Axis Auto Tuning System」과의 조합으로 가공정도와 안정성이 현격히 향상되었습니다.
또한 모두 곤란하다고 한 「가공 채터 방지」에 대해서도 최적의 가공조건을 즉시 이끌어내는 「Machining Navi」를 개발해, 채터 문제의 해결에 일조 및 긴 워크와 나사절삭 등에 불가결한 기능이 되었습니다.
약 20년간「Thermo-Friendly Concept」은 오쿠마의 독보적인 기술의 대명사가 되어, 2019년10월 현재로 전체 127기종 중 83기종에 탑재되어, 출하 대수는 5만대를 돌파했습니다. 그래도 세계의 공작기계 대수 중에서는 작은 숫자이며, 점점 고도화하는 「보다 빠르고, 보다 고정도의 가공을 」의 명제를 향해 지능화 기술의 한층 더 높은 곳을 추구해 갑니다.
- 이사/기술본부장겸 연구개발 부장
센다 하루미츠(SENDA Harumitsu) - 1987년 입사. 고베대학대학원 자연과학연구과 졸업, 박사(공학).
오쿠마 입사 후, 핵심 기술의 개발자로서 초정밀 가공 기술을 담당. 열변위 연구를 지원해, 주축의 열변위 보상시스템을 개발. 이것을 발전시킨 공작기계의 열변위 보상시스템으로 2002년도「일본기계학회상」 수상. 그 후에도 그룹 리더로서 열변위 제어의 연구개발을 비롯해, 지능화 기술 개발을 추진. 2011년에 연구개발 부장, 14년에 집행임원/기술본부 부본부장겸 가니(可児) 기술부장, 16년에 집행임원/기술본부장겸 연구개발 부장을 거쳐 17년부터 현직. 오쿠마의 기술・연구개발을 통괄한다.